One of the critical components of a construction project is an as-built drawing. As-built drawings provide a final record of the installed conditions, including all changes made over the course of a project.
As-built drawings are typically produced by general contractors and/or subcontractors at the end of a project, during the closeout phase. These are often referred to as final as-builts or for-record as-builts. Additionally, as-builts may be generated during the project to track design changes and deviations from the original plans.
In this article, we’ll cover everything you need to know about as-built drawings. We’ll start by answering common questions like “What are as-builts?” and “Who produces as-builts?” Then, we’ll explore what is typically included in as-builts and why they are crucial for construction closeout and handover to facilities teams. Finally, we’ll discuss how high-quality as-builts can improve your construction project.
What Are As-built Drawings?
An as-built drawing is a document used in the construction industry to provide a final record of the installed conditions, including all changes that occurred during the project. Typically, as-built drawings are provided at the end of the job as part of the closeout package. As-built surveys may also be conducted during the project to document any deviations from the original drawings.
Who Produces As-builts?
The original specification provided at the beginning of the project typically defines the as-built requirements. Many subcontractors are required to include as-builts as part of their closeout package. This is particularly relevant for trades such as:
- Mechanical
- Electrical
- Plumbing
- Fire protection
- Drywall
The specifications also define the format for the as-builts. While hand-written red-line drawings were once considered acceptable, advancements in construction technology have raised expectations. Design teams now often request as-builts in digital formats, such as AutoCAD, Revit, or IFC.
The design team, including architects and engineers, may also produce as-built drawings during the project to help track installation progress.
What Is Typically Included in As-builts?
As-builts can contain a wide range of information. They typically show the final locations of items such as piping, ductwork, and walls as installed on-site. These elements are often documented in 2D with dimensions and elevations. As-builts may also include product specifications and details like wiring diagrams and equipment layouts.
Why Are As-builts Important for Construction Projects?
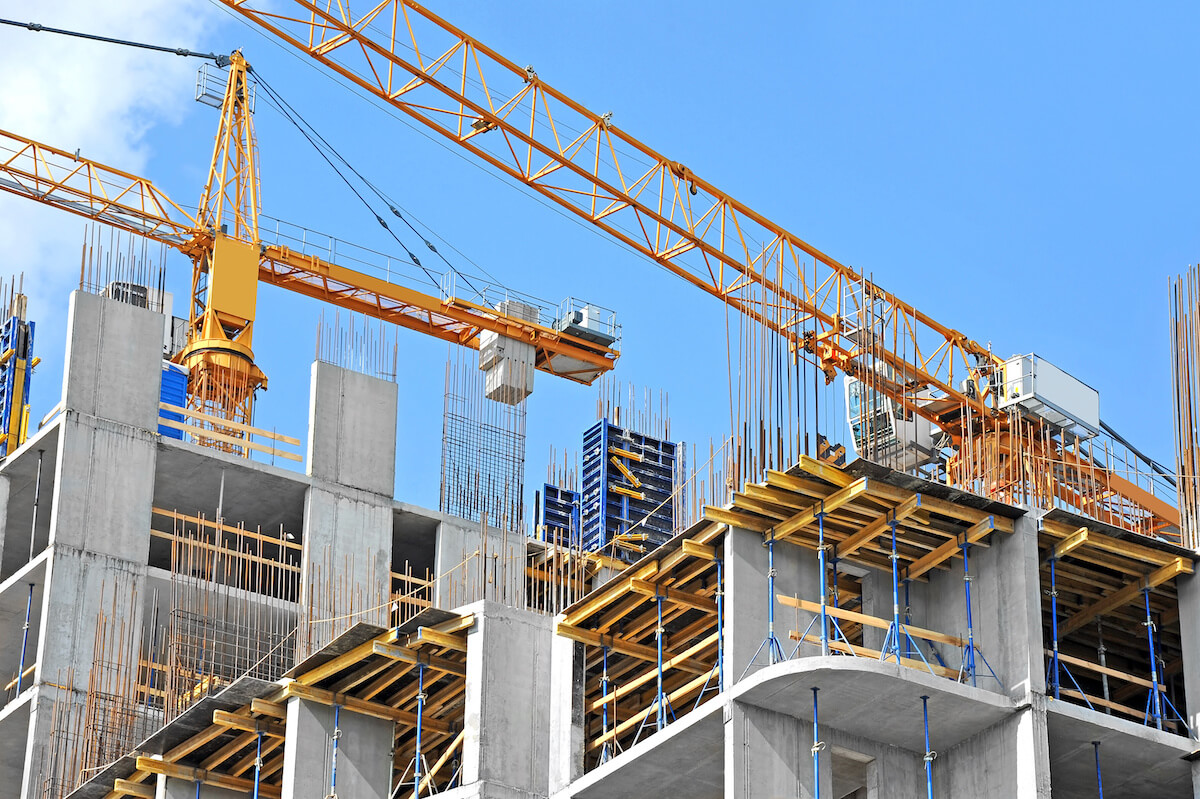
As-builts are essential for several reasons. First, they assist the end-user and facilities team once the building is handed over. Second, accurate as-builts help prevent waste and rework. Let’s take a closer look at both.
As-builts Assist the End User
Once a building is turned over, the maintenance team needs to understand where certain features exist within the systems. For instance, if they need to drain a portion of the mechanical system, they must know where the valves are located to perform this work. This is even more critical in an emergency.
While it might be assumed that this information is on the construction drawings, this is not always the case. Deviations from the original design often occur. Despite the best efforts of architects and engineers, every project usually has some scope gaps and changes to the issued documents. Additionally, design-build aspects of the project may have been completed without any drawings.
The facilities team may not perform maintenance work until years after project completion. In the example above, will the HVAC project manager remember where a valve is located five years after turnover? Probably not. Accurate as-builts ensure the maintenance team has an exact set of building plans for future reference.
As-builts Prevent Waste
As-builts aren’t just for the end of a project. They can also minimize waste and rework during the construction process.
For example, when renovating an existing space, an as-built scan of the existing conditions can be taken once the ceiling demo is complete. This scan allows for the coordination of above-ceiling MEP systems and the potential pre-fabrication of components, reducing wasted time and materials.
As you can see, as-built drawings benefit all stakeholders, from the design team to the end user.
How Can As-builts Help Improve the Overall Construction Process?
Too often, as-builts are considered an afterthought, thrown together haphazardly at the end of a project. By doing so, contractors miss an opportunity to streamline efficiency and reduce extra work.
Consider a project where you are renovating an existing space. If the mechanical contractor begins installing ductwork and notices the need for deviations to route around existing systems, this information could be relayed to the plumbing contractor through real-time as-builts. Without this information, the plumber might fabricate pipes based on the original plans, only to find them unusable once on-site.
The best way to maximize as-builts is by creating them in real time, in a file format accessible to the entire team, such as BIM. By taking a scan of the space, coordinators can run clash detection against the baseline model to identify potential issues early. These strategies are less feasible with manually red-lined as-builts.
Real-time as-builts help construction managers and design teams reduce rework, which is costly—typically 5% of the overall contract value—and can result in schedule delays. As-builts help track progress and improve efficiency.
As-builts Are a Vital Part of the Construction Process
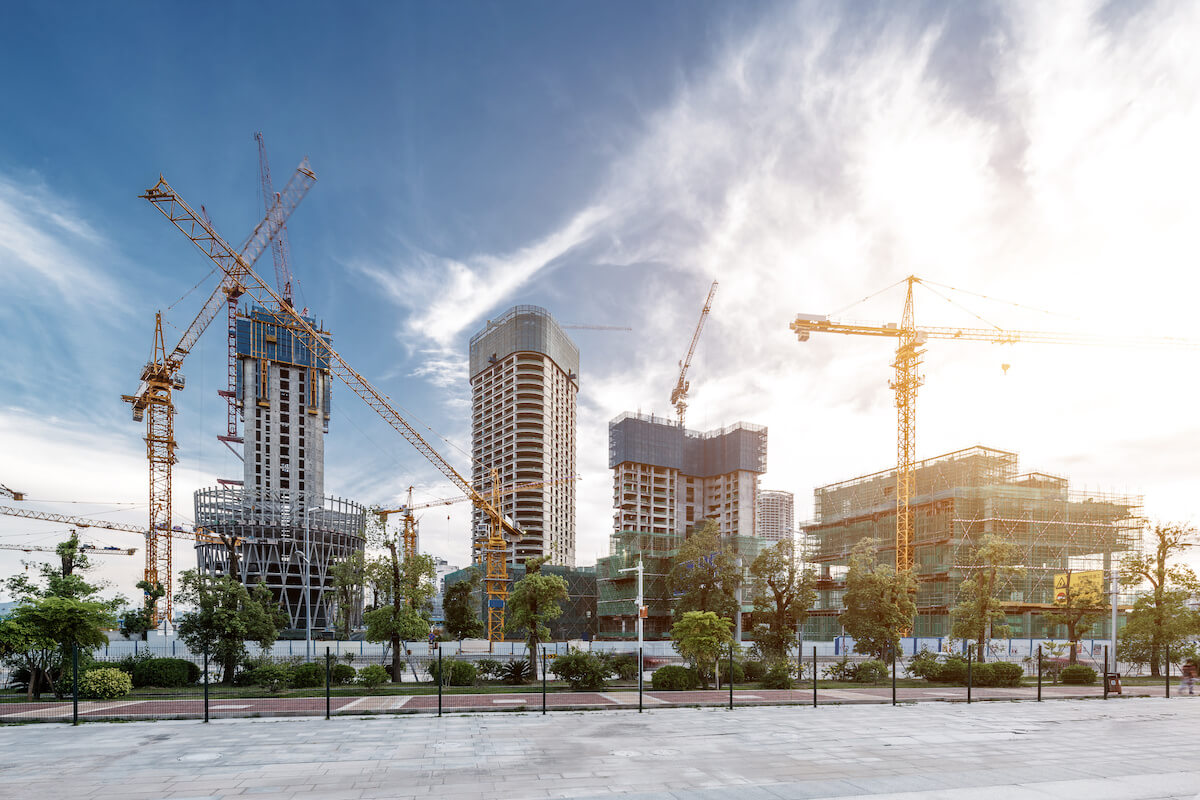
As-built drawings are a critical aspect of the construction process, often overlooked. They serve as essential for-record drawings for the building maintenance team and can prevent rework, especially when existing conditions need to be captured. Unfortunately, too many contractors still rely on paper, red-lined as-builts. That’s where Hexagon Building Solutions – Integrated comes in.
Hexagon Building Solutions is committed to transforming the architecture, engineering, construction, and owner (AECO) landscape by making technology matter. Our Construction Verification capability can streamline the as-built process in several ways. The As-built Verification workflow allows for automated deviation analysis so you can see changes from the original plans in real time. This workflow also promotes clash detection analysis and integrates with BIM, reducing the likelihood of rework and increasing the chances of staying on schedule.
Introduce Building Solutions to your jobsite so you can have complete knowledge of your build at any time. Learn more to get started.