Technology advances make 3D digital tank analysis effortless
Joel Hurt, Plant Business Manager for Leica Geosystems, explains why 3D laser scanning is replacing traditional approaches. Ever since the origins of tank storage, there has been a need to understand tank capacity and integrity. It’s not hard to imagine Jack Daniels and master distiller Nathan Green holding frequent discussions in 1864 about the volume and potential leakage of their kegs. Today, more than 150 years later, the same concerns that kept Nathan and Jack awake at night still keep those responsible for tank maintenance sleepless.
Fortunately, the methods used to analyse tank volume and integrity have advanced significantly. With 3D laser scanning, a non-contact and non-destructive method of digitally capturing physical objects in 3D using a beam of light, or laser, millions of measurement points can be captured on the tank’s surface. These combined points are known as a point cloud—a clear and precise digital record of the tank that can be used for analysis and maintenance.
Here are three reasons to consider switching to 3D laser scanning for your tank gauging process.
1. You need a fast and safe way to assess tank integrity
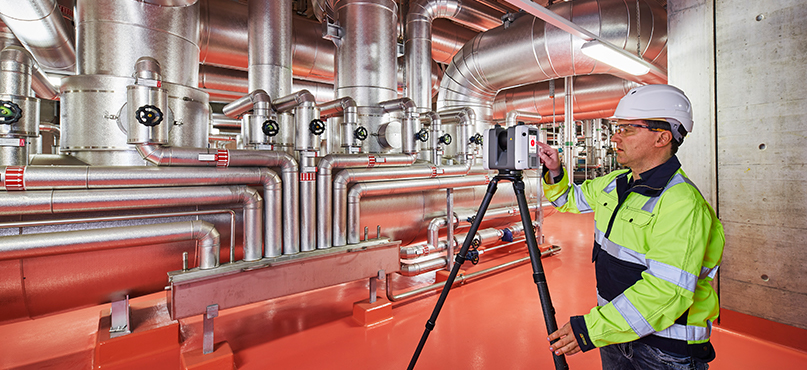
Traditional methods of float and tape tank gauging, servo gauging and hydrostatic tank gauging (HTG) work well enough for continuously measuring the level of product in the tank. However, they all have one critical limitation: They are unable to provide information on tank integrity. The only way you know you have a leak is through a loss of material, which can be costly.
Preventing leaks requires comprehensive tank inspections that can be completed quickly, accurately and safely. When a 3D laser scanner is used to capture or scan a tank from the outside, the entire tank can be captured in only four to six scans. Interior scans can be completed on out-of-service tanks in just one to two scans.
Because of the speed of 3D laser scanning, the time involved in tank inspections drops from weeks to hours— or even minutes. For example, the Leica RTC360, the fastest laser scanner available, completes a full scan in as little as 26 seconds. This means you can capture comprehensive tank data in a fraction of the time compared to other tank management methods.
2. You need a reliable way to reduce risk
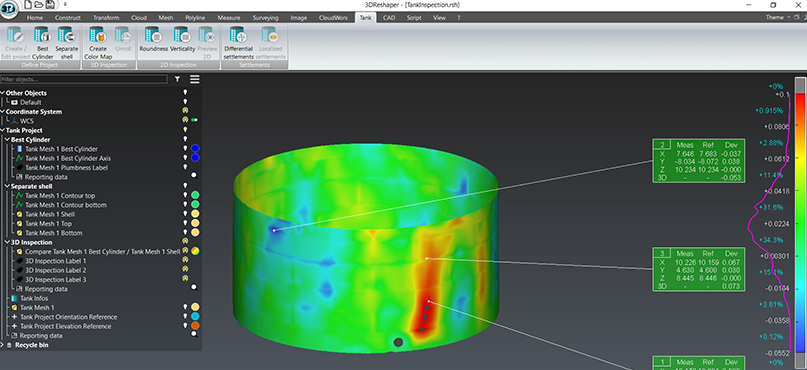
Timely tank inspections are key to identifying tank defects before they become major problems, but such inspections have historically presented their own risks. Using lifts, ladders and tape measures is hazardous and introduces the potential for errors and missed measurements.
Using 3D laser scanners with tank software, such as 3DReshaper Tank Module, enables you to identify problems early in tank maintenance processes. You can also:
- Automatically compute plumbness and the best cylinder of the tank
- Compute and customise a 3D colour map to inspect a tank
- Create labels to know the exact deviation on a given point
- Unroll the tank shell to display a 2D colour map
This is all done using API 650/653 tolerances. This advance intelligence reduces downtime and aids in averting fines. Additionally, it increases safety as virtually no climbing, no lifts or ladders are required.
3. You need an accurate record of existing conditions
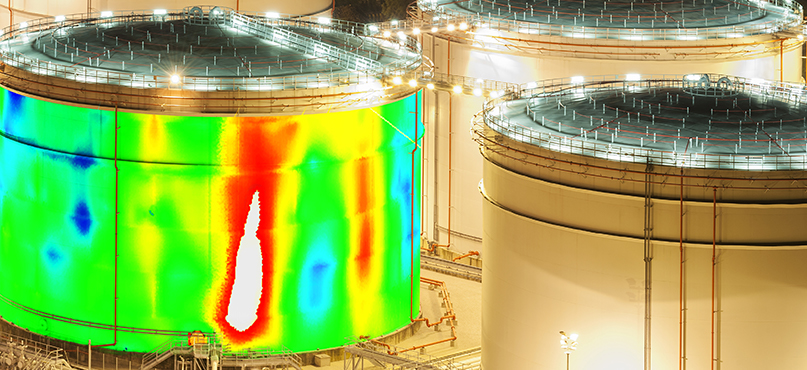
Comprehensive and up-to-date inspection records are crucial for environmental compliance in the oil and gas industry and are probably already part of your Spill Prevention, Control and Counter measure (SPCC) plan. But having a fast, easy and accurate way to create these records can also assist you with maintenance and future modifications, regardless of the product in your tanks.
3D laser scanning is the fastest, most accurate and safest way to capture tank data. Once captured, the data can be used for:
- 3D inspection
- Roundness
- Verticality and plumbness
- Tank modification projects
- Differential settlement
- Local settlement
- Deformation
For more information visit:
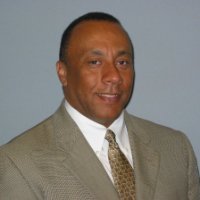
Joel Hurt, Jr.
Plant Business Manager
Leica Geosystems US/CAN